Personal Protective Equipment (PPE) – The Basics
July 3, 2014
The concept of personal protective equipment (PPE) most likely isn’t new to anyone who works in an industrial setting. The majority of safety managers and employees probably have to deal with some sort of protective gear like goggles, gloves or steel-toed boots on a regular basis.
Knowing how to start a PPE program, improve an old program or make sure your facility is compliant can get a little technical, though, so let’s take a look at what PPE standards employers need to follow and how they can most easily comply.
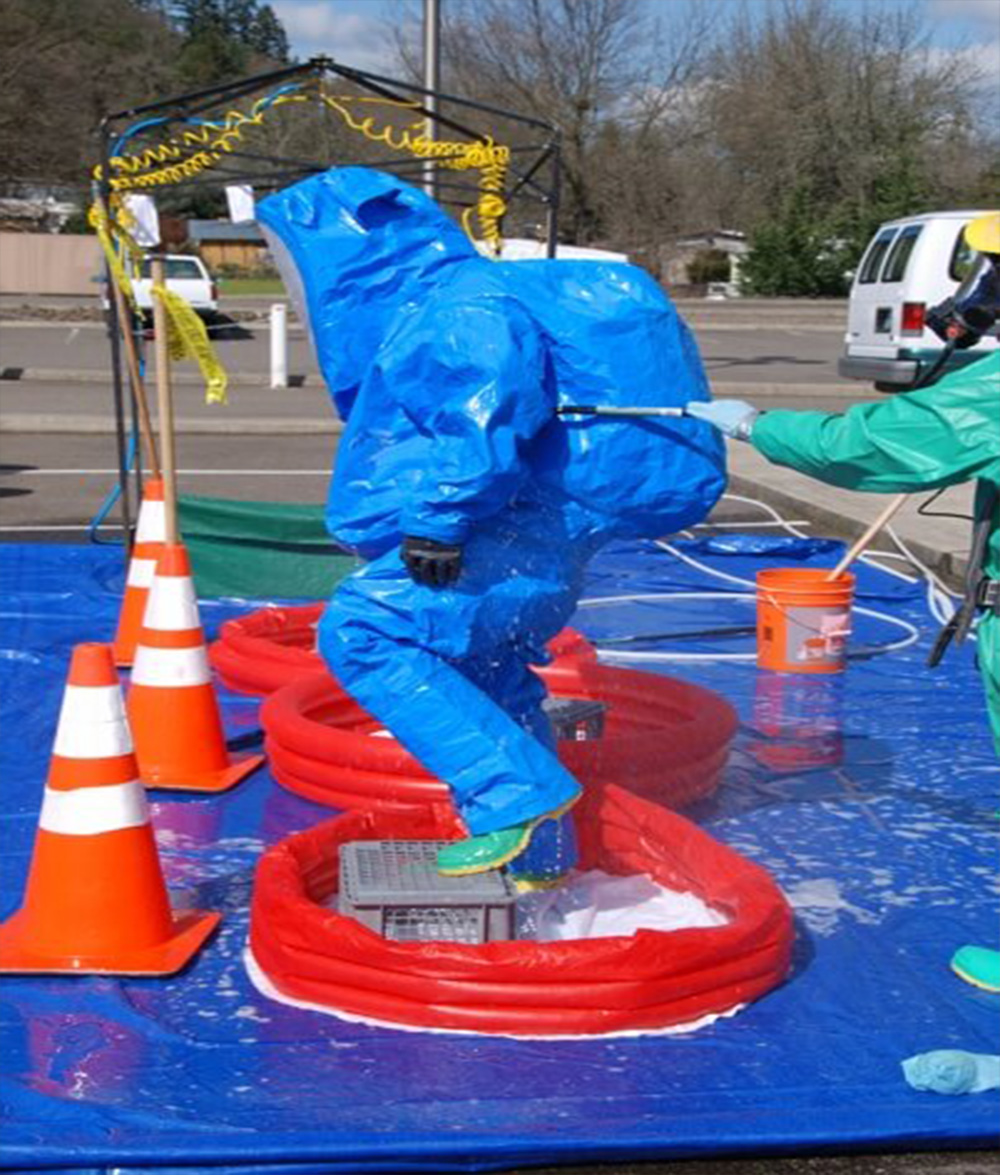
Assess Hazards that May Require PPE
OSHA has specific PPE-related requirements for employers, which are listed for general industry under OSHA standard 1910.132. (PPE requirements specifically for construction can be found under OSHA standard 1926.95.) The first requirement is that businesses must assess the safety hazards in their facilities to determine what types of PPE may be necessary for their workers.
During this assessment, OSHA recommends considering hazards related to impacts/collisions, compression (roll-over), temperature, chemicals, dangerous dust and lighting. Employers should note sources of electricity, sources of motion near machinery, places where objects could fall, sharp objects that could cause harm and biologic hazards (like blood or pathogens). They should also examine the facility’s past injury history (if it exists) to see if any patterns emerge related to hazards.
This hazard assessment can help safety managers and business owners make more accurate determinations about what types of PPE their facilities need. It’s important to keep in mind, though, that while PPE is often a key component of workplace safety, it should not be thought of as the primary means of hazard prevention:
“Using personal protective equipment is often essential, but it is generally the last line of defense after engineering controls, work practices, and administrative controls.”-OSHA
For those situations where engineering and procedural controls do not eliminate a hazard, you will need to select appropriate gear for your employees.
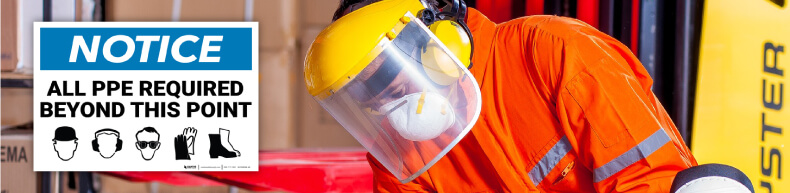
Types of PPE
Personal protective equipment is meant to protect workers from both physical and health hazards. According to OSHA, potential physical hazards include things like changing temperatures, moving objects or sharp edges, while health hazards include exposure to harmful chemicals, dusts and radiation. Many types of PPE exist, but most fall into one of the following seven categories.
Head Protection
Hard hats are necessary protective equipment, especially around construction and electricity. Hard hats can protect employees from impact hazards, penetration hazards and electrical hazards. If your employees work in areas where they could bump their heads against objects like beams, pipes or electrical equipment or where objects could fall from above, you need to provide them with hard hats.
Hard hats consist of a hard outer shell attached to the head with straps, and the design allows the hat to absorb shock. Hard hats must comply with ANSI Standard Z89.1-1986.
Hand Protection
Gloves are the most common type of hand protection and they can protect employees from hazards like chemical burns, absorption of harmful chemicals, bruises, cuts and fractures. Many types of gloves exist and they fall into four main categories:
- Fabric gloves and coated fabric gloves
- Chemical-resistant and liquid-resistant gloves
- Gloves made of leather, canvas or metal mesh
- Insulating rubber gloves (for protection from electrical hazards)
Assess the hazards at your work site; if your employees are not at risk of being exposed to hazardous chemicals but they are at risk of dropping heavy objects, for example, select gloves that aid with gripping rather than skin protection.
Eye and Face Protection
Employees encounter many eye and face hazards in the workplace. OSHA explains that these hazards include molten metal, flying particles, caustic liquids, liquid chemicals, chemicals vapors and gases, light radiation and possibly infected materials.
The most common type of eye and face protection is safety glasses, but safety goggles, face shields and welding masks may also be necessary. Eye and face protection must comply with ANSI Z87.1-1989. It is critical that this type of PPE fits employees well. If you decide to only purchase one set of eye/face PPE for a position (rather than one per employee), make sure employees clean the PPE after use.
Foot and Leg Protection
Foot protection like steel-toed boots can protect employees from hazards like falling or rolling objects, hot surfaces and corrosive materials. In addition to steel-toed boots, other common types of PPE for the feet and legs are leggings (which are made from a strong material like leather and protect the lower legs), toe guards, safety shoes (which have impact-resistant toes and heat-resistant soles), electrically conductive shoes (to prevent static buildup) and nonconductive shoes (for working near electrical hazards).
Hearing Protection
Earplugs and earmuffs are the common types of hearing prevention used at industrial worksites. Many times workers overlook hearing hazards because they think the duration of the noise won’t cause injury, but the louder a sound, the more quickly it can damage hearing.
If your worksite poses a threat to workers’ hearing, be sure to provide them with this type of PPE and consult OSHA standard 1910.95 for more information about occupational noise exposure.
Body Protection
Many conditions on the jobsite can warrant full-body protection such as safety suits, aprons and visibility vests. Extreme temperatures, hot liquids, dangerous chemicals and impact hazards related to machinery and tools can all mean this type of PPE is needed.
The material this PPE is made from will depend on the hazards present. For example, fire-resistant cotton or leather may be best for employees working near open flames, while duck—a closely woven fabric—may be most appropriate for employees at risk of cuts from moving sharp materials.
Respiratory Protection
Respiratory protection is essential in situations when employees may be exposed to anything harmful in the air like dust, fumes, gases, smoke or vapors. Respirators and facemasks cover the nose and mouth and must fit properly for them to work. Make sure to select models approved by the National Institute for Occupational Safety and Health (NIOSH) and evaluate the fit of the PPE before allowing an employee to use it.
OSHA provides detailed information about respiratory protection under standard 1910.134, as well as in publication 3079, so consult these documents for more assistance.
Selection Criteria
In addition to selecting the appropriate types of PPE for your workplace, you also need to make sure you select options within that category that sufficiently address the hazards present. Some categories of PPE are made up of products with different levels of protection, so first decide what amount of protection you need. (For example, there are Type 1 and Type 2 hard hats, as well as helmets made to withstand different levels of electricity.)
If you’re concerned about selecting PPE that really does what it claims, see if the manufacturer or supplier put the product through rigorous tests. New ANSI/ISEA standards came out in 2014 for PPE testing, so you can learn about the quality of products based on the level of testing certification those products have.
After you’ve decided which models of PPE and levels of protection your workers will need, you must also consider the sizes of the equipment. PPE that doesn’t fit properly will not protect workers as well as it should. For some types of PPE like respirators or facemasks, the wrong size equipment can prevent the PPE from working at all.
When appropriate, select the correct size for each employee. If equipment will be shared, make sure that it is labeled with its size or that it can be easily adjusted.
Finally, consider the comfort level of PPE. Employees are much more likely to wear PPE if it’s comfortable because it won’t irritate skin and employees won’t feel like the PPE gets in the way of their jobs. Sometimes this means choosing slightly more expensive equipment, but in the long run that money will likely be worthwhile if it means employees will actually use the gear.
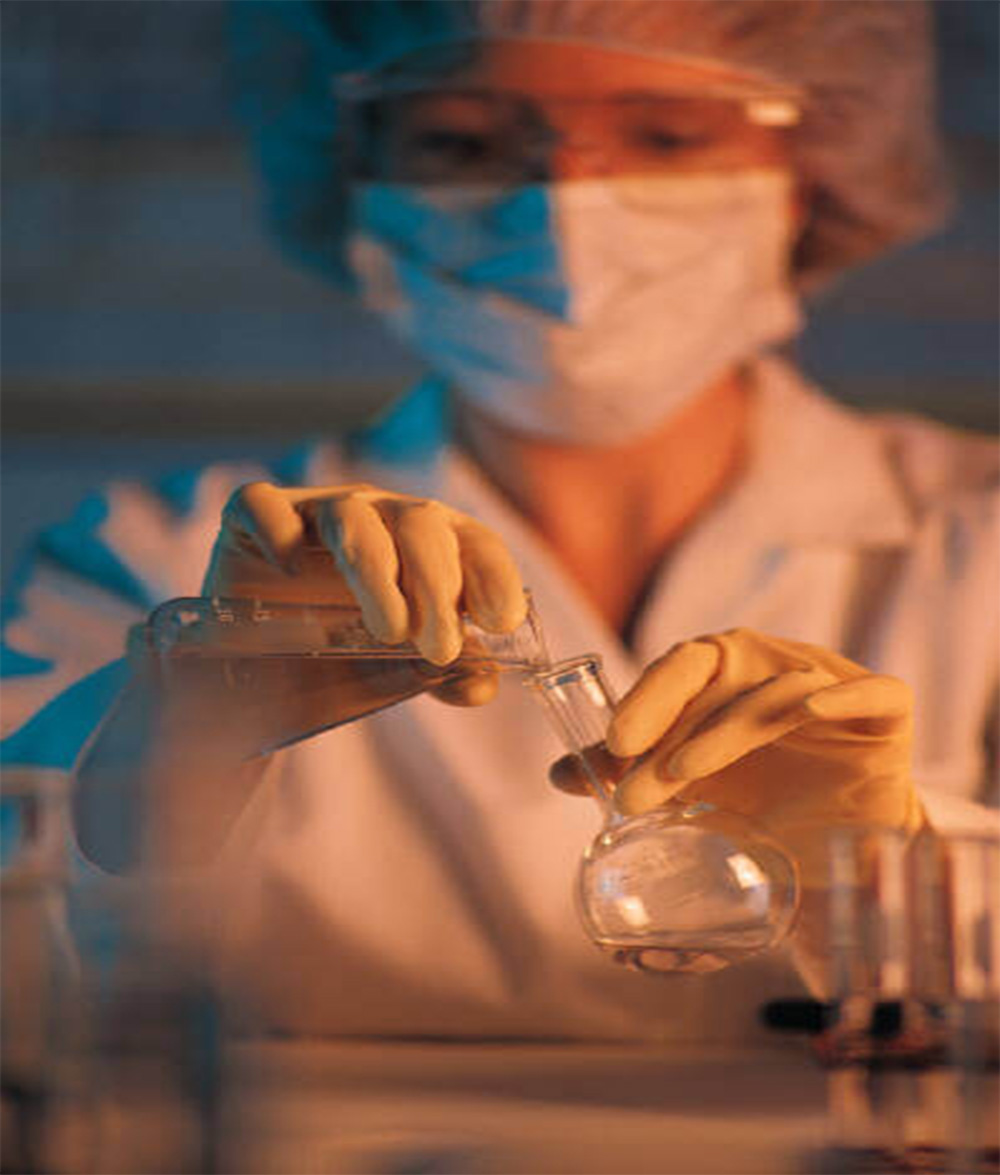
Paying for PPE
There are a few exceptions to the rule that employers must pay for PPE. The following items are excluded from the rule:
- Non-specialty protective footwear and non-specialty prescription safety eyewear (if this gear can be worn away from the job site)
- Everyday clothing
- Ordinary items for weather protection like coats, hats, sunglasses and sunscreen
- Lifting belts
- Hair nets and gloves worn by food workers
- Replacement PPE if the employee lost or purposefully damaged the old PPE
OSHA requires that employers pay for most PPE and provide it to employees at no cost. In some cases, employees may use their own PPE, but employers cannot require this and they are still required to check employee-provided PPE to make sure it works.
Employee Training
Before sending new PPE out into the workplace, employers are also required to provide proper training for employees. This means employees need to know when to use the equipment, how to use it—including how to put on, adjust, wear and remove it—and maintain the equipment. Maintaining the equipment should involve disinfecting (if applicable), checking for wear and tear and informing a supervisor if the PPE is dysfunctional or needs replacing.
Employees should also understand the limitations of PPE. They need to know under what circumstances the PPE will keep them safe and when they should change their behavior because they are in danger.
Conduct new training whenever PPE changes and whenever an employee appears to not fully understand PPE requirements. Getting feedback from employees about the effectiveness of PPE can help you improve your PPE program, too.
Safety signs and labels reminding employees when and where to use PPE can also help keep workers safe on the job, so consider adding visual cues to your facility.
For Reference: OSHA Regulations
For General Industry:
- 1910.132: General Requirements and Payment
- 1910.133: Eye and Face Protection
- 1910.134: Respiratory Protection
- 1910.135: Head Protection
- 1910.136: Foot Protection
- 1910.137: Electrical Protective Devices
- 1910.138: Hand Protection
For Construction:
- 1926.28: Personal Protective Equipment
- 1926.95: Criteria for Personal Protective Equipment
- 1926.96: Occupational Foot Protection
- 1926.100: Head Protection
- 1926.101: Hearing Protection
- 1926.102: Eye and Face Protection
- 1926.103: Respiratory Protection
Additional Resources
- PPE: Personal Protective Equipment [Safety Standards]– creativesafetysupply.com
- Stay Safe and Warm with Personal Protective Equipment (PPE)– realsafety.org
- A Brief Introduction to Personal Protective Equipment– babelplex.com
- Keeping Personal Protective Equipment (PPE) Clean– creativesafetypublishing.com
- Personal Protective Equipment, Ensuring Full Protection at Work– blog.creativesafetysupply.com
- What is PPE? – 10 Ways to Protect Workers– blog.labeltac.com
- Keep an Eye on Safety with ANSI z87.1– hiplogic.com
- PPE Training is a Must– aislemarking.com
- Workplace Safety & Foot Protection– lean-news.com